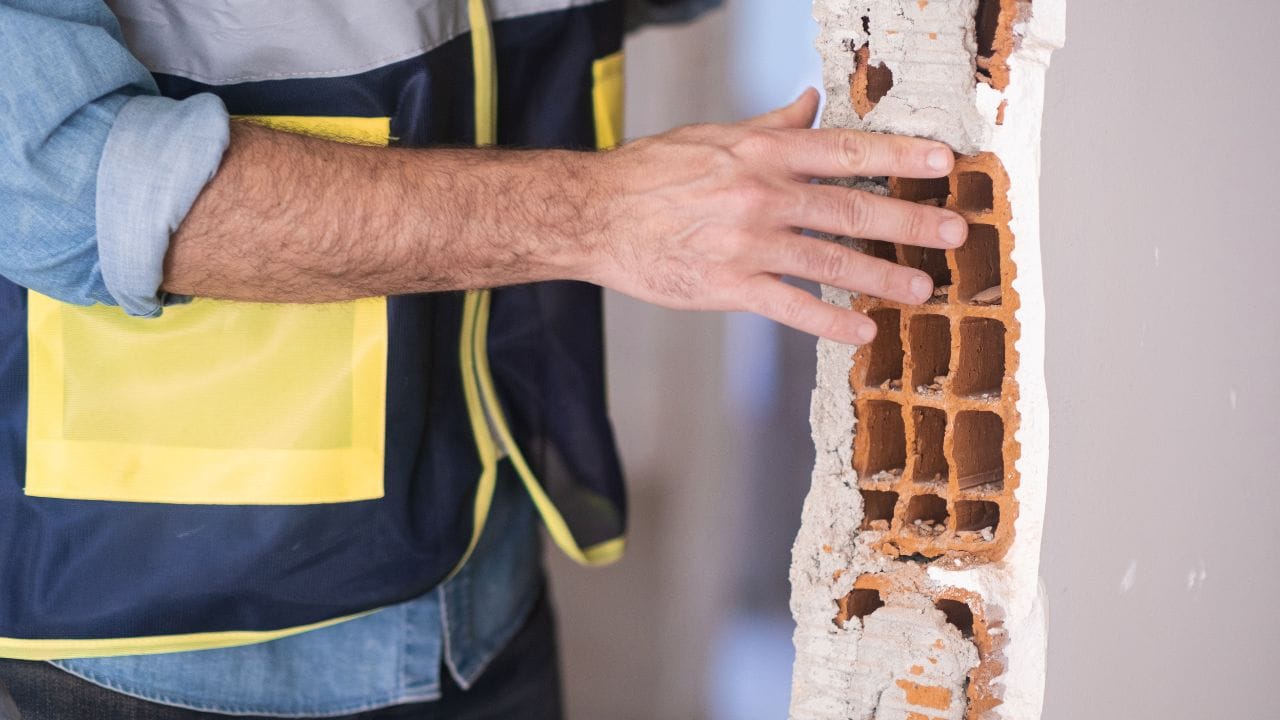
17 Oct How to balance cost and quality in the construction industry
Balancing cost and quality in the construction industry is a constant challenge for all parties involved in any construction project. This challenge grows as projects and infrastructure become more complex, customer expectations are higher, and economic conditions change. It requires a deep understanding of the factors that affect both cost and quality and the ability to make strategic decisions to achieve goals.
This article will discuss how to balance cost and quality in the construction industry, reviewing the factors affecting cost and quality, the importance of proper planning, and successful implementation strategies.
1. Understanding the relationship between cost and quality
The balance between cost and quality are two closely related themes in the contracting industry. It is essential to understand that low cost does not necessarily mean low quality, and vice versa. Achieving high quality at reasonable costs may be possible if resources are used efficiently and waste is avoided.
- Direct cost versus indirect cost: Direct cost includes the materials, labor, and equipment used in the project. Indirect costs include administrative and maintenance costs. Striking a balance requires managing expenses to achieve the required quality without overspending.
- Required quality versus acceptable cost: The level of quality needed should be determined at the beginning of the project based on the client’s requirements and usage needs. This helps in making accurate cost estimates and looking for options that meet the quality requirements within the given budget.
2. The importance of planning ahead
Planning is the key factor in balancing cost and quality in any contracting project. Good planning allows contractors to identify potential costs and options to get the best quality at the lowest possible price.
- Prepare a detailed budget: An accurate budget helps avoid financial surprises during the project. The budget should include all the details associated with the project, including materials, labor, administrative costs, and the expected cost of future maintenance.
- A detailed feasibility study: Before starting any project, it is necessary to conduct a thorough feasibility study to analyze the potential benefits and associated costs. This study helps determine the scope of the project and the resources required and identify suitable alternatives that meet the requirements at the lowest price without sacrificing quality.
- Create a realistic time plan: Time planning contributes to cost optimization. Delays in project delivery lead to increased indirect costs, such as labor and equipment costs. Therefore, it is essential to develop an accurate time plan and stick to it to ensure the project is delivered on time and within budget.
3. Choose materials and suppliers wisely
The materials used in construction play a huge role in determining the final quality of the project as well as the cost. The search for cost savings does not mean choosing the cheapest materials but choosing the best balance between price and quality.
- High-quality, cost-effective materials: It’s essential to look for resource-efficient building materials that minimize cost in the long run. For example, using more extended materials may increase the initial price but save money on future maintenance and repairs.
- Choose your suppliers carefully: A good supplier can provide competitive-quality materials. Contractors should invest in establishing long-term relationships with reliable suppliers to ensure that the materials required are high quality and cost-effective.
- Negotiate for competitive prices: Contractors should be skilled at negotiating with suppliers to ensure they get the best deals in terms of quality and cost. Buying in bulk or dealing with the same supplier for multiple projects can minimize expenses.
4. Technology and its role in achieving balance
Modern technology plays a massive role in the contracting industry, effectively balancing cost and quality. The use of technology contributes to improving efficiency, reducing costs, and increasing the quality of the final project.
- Design and engineering software: Computer-aided design (CAD) software can improve design quality and minimize human error. This leads to cost savings by reducing on-site adjustments and improving coordination between all parties involved in the project.
- Technology in project management: Advanced project management systems help track project progress and manage costs and quality simultaneously. These systems provide accurate reports on work phases and allow for immediate adjustments in case of any changes.
- Utilize modern construction techniques: Technologies such as 3D printing, lightweight structures, and renewable energy in projects reduce costs and increase efficiency. These technologies offer innovative solutions to achieve high quality while reducing costs simultaneously.
5. Human Resource Management
Labor is one of the most crucial cost elements in any construction project, but it is also a critical factor in the quality of execution. Effective human resource management helps balance cost and quality.
- Choose qualified labor: Skilled labor may be more expensive, but it improves the quality of work and reduces errors that can increase costs. Investing in training workers to increase their competence increases the chances of achieving better quality at a lower price.
- Manage labor effectively: Time and resource management systems can help reduce costs by improving productivity and ensuring timely tasks. Good planning of daily tasks minimizes wastage of time and resources, lowering overall project costs.
6. Smart contracting and risk management
Contract and risk management is an essential part of balancing cost and quality. Smart contracts and proper risk management planning can minimize unexpected costs and improve project quality.
- Performance-based contracts: Using performance-based contracts or project delivery based on specific milestones rather than full-time can help improve the quality of work. Such contracts incentivize contractors to adhere to high-quality standards and avoid delays or failures that could lead to additional costs.
- Risk management: Every construction project carries with it potential risks, whether it’s related to resources, schedule, or even local laws. By analyzing risks and identifying preventative solutions, costs that arise from delays or unforeseen issues can be minimized.
7. Quality Inspection and Testing
Balancing cost and quality requires a practical inspection and quality control system to ensure all project phases are carried out to the required standards.
- Regular inspections: Regular inspections throughout the project help identify and correct issues early before they escalate. This method reduces the final cost by minimizing the need to rework or fix mistakes.
- Final quality testing: Performing quality tests at the end of each construction phase ensures that the materials and methods used meet the required standards. Regular testing reduces the likelihood of future issues, minimizing the costs associated with maintenance or repairs.
8. Sustainability and innovation for a better balance
Sustainability has become a key criterion in the modern construction industry, balancing cost and quality as more contractors turn to sustainable solutions that save long-term costs and improve project quality.
- Sustainable building materials: Using materials that rely on renewable resources or minimize energy consumption reduces long-term costs and improves the quality of life for the project’s beneficiaries. For example, solar or thermal insulation can reduce operational costs and improve quality.
- Innovation in construction techniques: Adopting modern construction techniques such as robotics or 3D printing allows for better quality at a lower cost by minimizing resource wastage and improving execution accuracy.
Conclusion
Balancing cost and quality in the construction industry is a complex process that requires good planning, effective resource management, and modern technology. A perfect balance between cost and quality can be achieved by focusing on advance planning, selecting the right materials, and employing skilled labor. Innovation and the use of sustainable technologies are also an important part